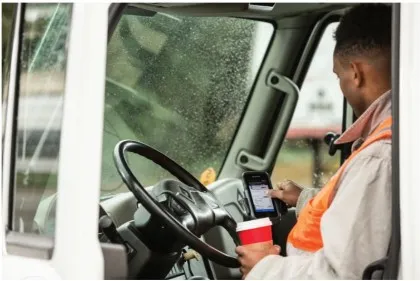
Overcoming the last-mile challenge
Having an effective last-mile strategy starts from the warehouses and distribution centres (DCs).
With today’s complex supply chains, visibility and orchestration are key. The last mile makes up 50% of total logistics costs, according to Honeywell, and there are many challenges found in this segment of the supply chain.
For example, companies have to deal with congestion in urban areas and distance in remote areas. They are also compounded by practical issues such as invalid or incorrect address details and delivering to hard-to-locate locations. Sometimes no one is home to accept the delivery or there may be buyer’s remorse as customers may not want the purchase anymore. Additionally, there may be local infrastructure issues to deal with such as the lack of nearby parking and elevators which are out of service.
All these factors add cost, time and inconvenience to an already marginal activity.
Starting in the warehouse
Sometimes, the problems with the last mile are linked back to the DCs and warehouses. “The delivery and distribution processes are tied together and closely connected,” says Lynn Huang, head of marketing and strategy for Honeywell Safety and Productivity Solutions, ASEAN & ANZ. “For the last-mile delivery to take place, things have to happen within the four walls to ensure that the packages are picked correctly, include the right type of information (such as delivery labels, correct addresses and so on) and meet delivery windows.”
It is also beneficial to move away from manual and paper-based warehousing systems as a starting point to make strides in improving last-mile deliveries. “It all starts in the DC, where anything that is being done on paper is slower and wrought with errors. When you work off paper, you are working more slowly than you would be if you were using directed system input, mobility devices, scanners and/or voice,” she said.
For example, Honeywell offers its Operational Acuity analytics software to help businesses get a clearer picture of their warehouse operations to keep digital and physical movements parallel. The software uses data collection, aggregation and predictive modelling techniques for detailed and powerful data analysis. It helps to make sense of the vast amount of data available from a workflow environment, says the company, making it an ideal operational intelligence for a more efficient and productive business.
Connecting workers
To improve the last-mile hurdles mentioned, delivery workers must become connected workers. This involves equipping workers in the field with handheld computers as well as other connected mobile devices such as rugged portable receipt printers and wearable scanners.
According to Honeywell, postal and delivery firms of all sizes are deploying these mobile solutions for their workforce. For example, the Jersey Post Group, service provider of mail service for the Bailiwick of Jersey in the UK, experienced a 196% increase in parcels handled since 2007. To meet these challenges and create new revenue streams, it turned to Honeywell technology to help extend robust track-and-trace capabilities across its entire network.
“The decision to employ these new [Honeywell Dolphin CT50] handheld computers is a significant step forward in our programme of investment and innovation to provide the best customer service and to improve the working experience of our employees,” says Andy Jehan, director of operations, Jersey Post.
The new mobile devices, along with updated tracking solutions, enabled Jersey Post’s workers to provide greater visibility into the delivery process to consumers and business partners. The solution also increased the responsiveness of the delivery services team and allowed Jersey Post to add additional services to meet growing consumer demand for more responsive delivery. Hence, the technology investments gave Jersey Post staff and customers a clearer view of the progress of an item, from receipt through to delivery.
Moving to the cloud
With increased demand in traceability of the delivery process, it is important to ensure that packing and loading, as well as proof of delivery, are traceable. Honeywell’s Movilizer platform is a cloud-based solution that allows businesses to connect their mobile workers to back-end systems to improve customer service, sales and operations. One of Movilizer’s offerings is a proof-of-delivery app to maximise visibility and intelligence with asset utilisation.
In fact, the solution enabled a large range of global companies to set up their global tracking strategies. All of these companies have been able to leverage the cloud and draw on the cross-functional knowledge and expertise within Movilizer to reduce complexity and cost. These projects cover the full range of serialisation and asset utilisation capabilities — from regulatory compliance to product interaction to transparency.
Increasing fleet uptime
Effective fleet utilisation plays a key role in last-mile success. In today’s fast-paced environment, documenting inspection and maintenance checklists for vehicles prove to be typically inefficient because they force technicians to enter their observations as a separate step from the inspection process.
To move towards voice-enabling and streamlining processes, Honeywell Vocollect voice solutions can help elevate documentation and compliance in the maintenance and inspection operations.
Not only does it maximise the technician’s procedures, but it also virtually eliminates the cumbersome and inefficient steps traditionally associated with previous generation technology alternatives. The “Hands-Free, Eyes-Free” ability enhances the documentation of standard operating procedures and provides the continuity needed for better consistency across all locations. By using Vocollect to conduct maintenance tasks on vehicles as they fulfil last-mile deliveries, the maintenance and inspection solution will play a part in increasing fleet uptime.
Planning visibility
There is an increased need to drive orchestration across all related parties to improve visibility in supply chains and speed of delivery. When end-to-end management of inventories and transportation, distribution and overall logistics execution are optimised, they bring a secure way of integrating subcontractors and customers, as well as internal systems and operators. According to Huang, by making improvements to tackle last-mile transportation challenges, companies will reap benefits such as cost savings, fewer product returns, better visibility, happier customers and more streamlined supply chains. To find out more information about Honeywell’s solutions, please visit https:// retailsolutions.honeywell.com/ or email [email protected].